Factory Automation News

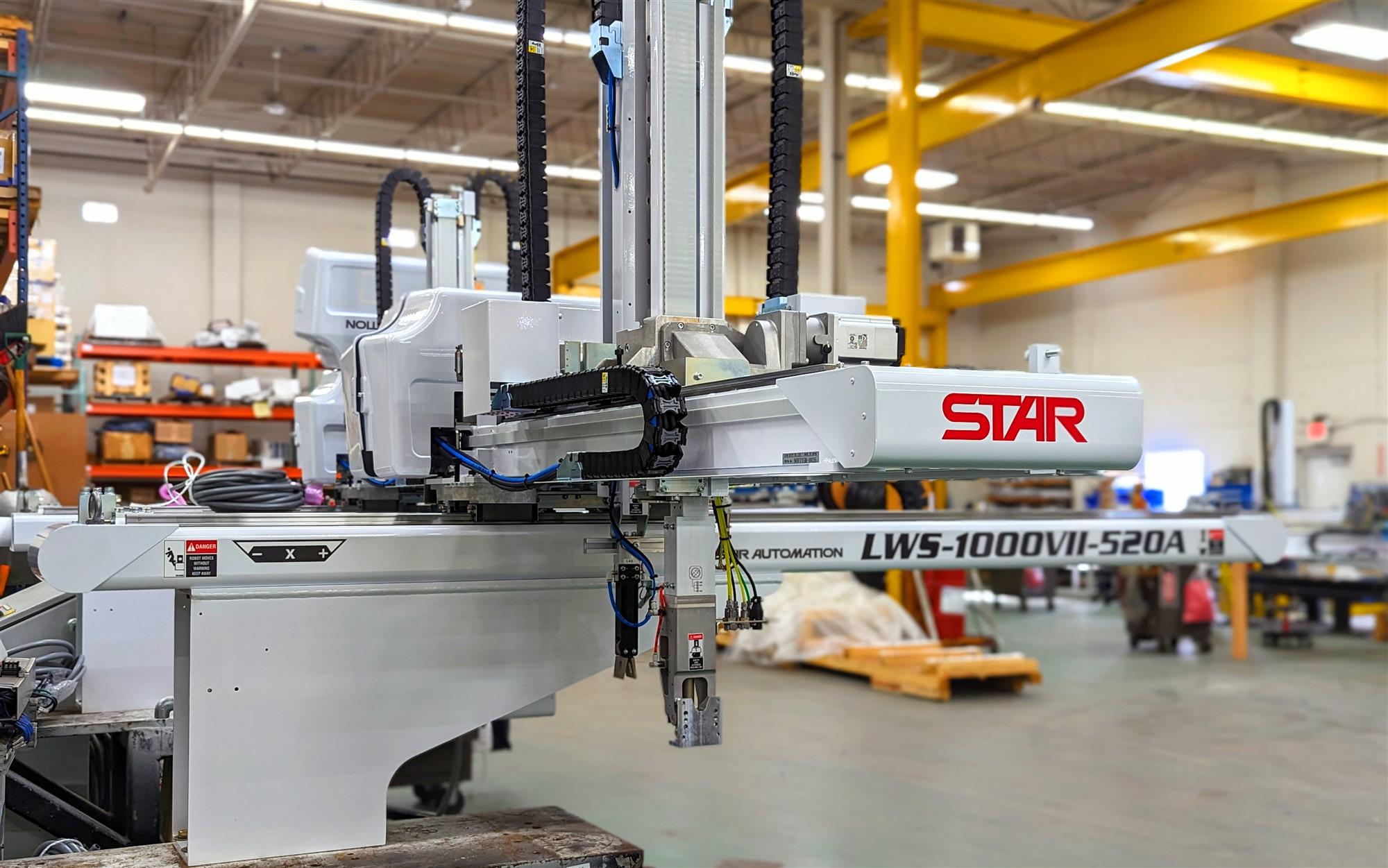
Optimizing The Injection Molding Process
Injection molding is a widely used manufacturing process for cheaply and efficiently producing large quantities of plastic components. In this process, molten plastic is injected into a mold, where it is then cooled and solidified and then removed from the mold. Finding ways to optimize injection molding processes to make them more efficient, cheaper, and safer is always a high priority for managers of injection molding factories. For these reasons, automation is becoming increasingly popular in the injection molding industry as it allows for increased efficiency, more consistent quality, less labor costs, and a safer work environment.
In this article, we will explore how automation can be implemented into the injection molding process to optimize efficiency, cost, and quality.
The Importance of Automation in Injection Molding
A key benefit of automation in injection molding is the ability to increase speed and efficiency. Automated systems can run continuously, handle multiple tasks at once, and package and ship projects. These features allow for increased productivity and speed as opposed to relying on manual labor.
Additionally, automation allows for accurate reproduction and consistency in the final product. As automated systems perform programmed instructions almost exactly the same every single time, the resulting products are identical in size, shape, and material properties, eliminating human error from the process. This ensures that every part produced meets the exact quality standards and specifications required.
Types of Tools Used for Automation in Injection Molding
There are several different types of tools used to help automate an injection molding operation. Each plays a unique role in automating certain steps of the process.
Servo Robots
Servo robots are the most general robot used for automation in injection molding. Servo robots are most commonly used to take the completed part out of an injection molding machine after it hardens. These robots can then place the finished part into a bin or bucket, or onto a conveyor to be transported to a new location. Although their functionality may seem simple, their flexibility allows them to adapt to a wide variety of tasks and because they complete the task identically each time.
Sprue Pickers
One of the most common types of automation found in injection molding facilities, sprue pickers are responsible for removing the sprue from an injection molding machine, the extra plastic that hardens inside the channel’s where it is pumped into the machine. They can be adjusted to either cut the sprue off of the part, or fetch the sprue from the machine. After removing the sprue, the sprue picker sets it aside in a bin where it can then be recycled.
Conveyers
Conveyers are the tool that brings the whole process together. In order to link automated steps together, conveyers are required to move parts and materials throughout a factory so that they can be picked up by other robots or automation technology.
Pallet Changers
Pallet changers help facilitate an efficient exchange of molds or tooling being used in or with an injection molding machine. They help increase the efficiency of an injection molding process by cutting down on time finding and transporting different molds or tools and allowing for quick adjustments.
What to Consider When Automating Your Injection Molding Operation
Automating your injection molding operation may seem like a large task and it certainly is, however, it is one that is worthwhile. There are many things to consider, but some of the most important things are:
- Identifying Steps that Can Be Automated: The first thing to consider is what steps you want to automate. Although automation is an extremely valuable tool, some steps may not be suitable to automate. Research different tools that can be used to automate parts of the process and determine what steps you want to automate and how you are going to automate them.
- Evaluate Return on Investment: Although automating an injection molding operation comes with many benefits, it is still important to make sure that it makes sense for your situation. Run the numbers to make sure that the investment makes sense before committing to the investment.
- Develop a Detailed Plan: Developing a detailed plan before purchasing automation equipment is important to insure that your implementation process goes smoothly. Make sure that you know how you are going to install the equipment and train your employees ahead of time in order to reduce downtime and installation time.
- Training Employees: One of the most important parts of the installation process is to ensure that your employees know how to operate the equipment and operate it safely. In addition, think about how your employees roles will be changed or impacted by the new automation.
How to Start Automating Your Injection Molding Operation
With the many benefits of automating your injection molding operation, it’s obvious why you may want to start your journey to an automated injection molding operation. However, there are many things to consider and roadblocks to avoid. Star Automation’s engineers have helped countless injection molding factories automate their process and will be by your side to walk you through the process of choosing what steps to automate, what equipment to buy and implementing the equipment.