Factory Automation News

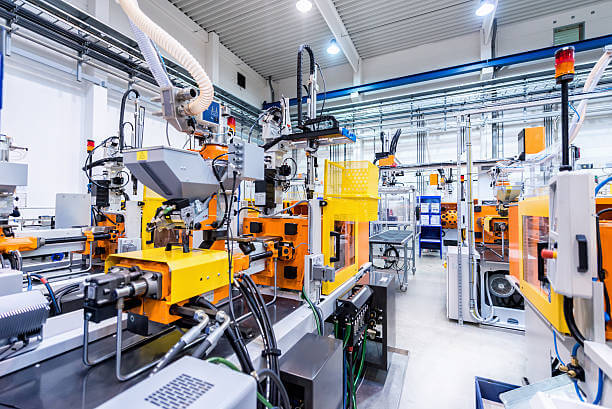
Automation in Injection Molding: Planning and Implementation
Injection molding is one of the most efficient and cost-effective ways to produce high-quality plastic parts in large quantities. As plastic is one of the cheapest materials for parts and has many uses, the demand for plastic parts continues to grow. Because of this, it is essential for manufacturers to find ways to increase the speed and efficiency of their injection molding process. Implementing automation is the easiest way to accomplish this, and also comes with other cost-saving benefits.
In this article, we will discuss key considerations throughout the planning and implementation process of automation in an injection molding plant.
Why Automate Injection Molding?
Automating the injection molding process has several benefits, including:
- Increased Speed and Efficiency: Automating injection molding machines allows them to operate and faster speeds and with more precision than manually operated machines. This allows manufacturers to produce more parts in less time.
- Improved Product Quality: Automating your injection molding machines allows them to maintain consistent, precise temperatures and pressure, resulting in more consistent and higher-quality parts.
- Reduced Labor Costs: Automated injection molding processes reduce the need for manual labor, leading to significant cost savings for manufacturers.
Planning for Automation
Automating an injection molding plant can feel stressful. Having a plan is essential in order to ensure that your implementation goes smoothly. Some key considerations to make while you are planning include:
- Identifying Specific Steps to Automate: Although automation can greatly increase efficiency, not every step is suitable to be automated. Research different automation technologies like sprue pickers, servo robots, and conveyors and analyze your current process to figure out where these technologies fit in.
- Determining Necessary Equipment: After you identify the steps that you would like to automate, you must next determine what equipment you need to automate them. Although you likely know what type of technology you need for each step, carefully consider what models work best for your operation. Some specs to consider are the vertical, traverse, and crosswise stroke, size, and range of IMM the equipment is suitable for.
- Evaluate Cost and Return on Investment: Automating an injection molding plant is a significant investment, but it is almost always a worthwhile one. However, it is crucial to run the numbers for your own situation and make sure that the investment makes sense for you.
- Develop a Detailed Implementation Plan: Once you have identified the steps you want to automate, the equipment you are going to buy, and confirmed that the investment makes sense, the last step is to develop an implementation plan. When drafting your plan, make sure to include timelines, milestones, and responsibilities.
Implementing Automation
After the planning phase is complete, manufacturers can start the process of implementing automation into their injection molding plant. Typically, this process includes the following steps:
- Installing and Setting Up Equipment: The first step in this process is to unpack, set up, and program your new equipment. This is the biggest step of the process, but also the most important. Getting all of your equipment set up and programmed properly will set a good foundation for the rest of the implementation process and reduce headaches down the line.
- Testing and Debugging: Before you start training employees or production, testing and debugging your injection molding process is vital to insure that it is operating properly. Thoroughly testing your new equipment will help you catch errors and production quality issues before they negatively impact your production efficiency.
- Training Employees: After you finish setting up your new equipment, it is important to make sure that employees are properly trained and understand how to safely use the new equipment in order to maintain a safe work environment. In addition, training your employees on their new roles or how their roles changed is essential to keeping efficiency and employee morale high.
- Monitoring and Optimizing Performance: Once you finish these steps and start production with your new automated injection molding process, all that is left is to monitor and optimize the performance of the new process. By monitoring and finding pain points of the new process, manufacturers can unlock further increases in efficiency in their process.
How to Start Automating Your Injection Molding Plant
Automating your injection molding process can bring significant benefits including increased production speed, efficiency, and product consistency, and decreased labor costs. However, properly planning and implementing automation into your injection molding plant is essential to ensure that you maximize the benefits and minimize costs. Although planning this process may seem difficult, Star Automation’s expert engineers have helped automate countless injection molding operations and can help guide you through yours.
Contact a Star Automation representative to discuss injection molding automation solutions for your factory.